Project Brief
The aim of this case study was to perform a comprehensive 3D steady-state CFD analysis of diesel generator systems to evaluate the temperature, pressure, and velocity distribution. The project involved assessing heat dissipation from various components and identifying potential temperature hotspots to ensure optimal performance and longevity of the DG systems. By leveraging advanced CFD techniques and modeling, the study aimed to provide valuable insights into the thermal management and airflow characteristics of the system.
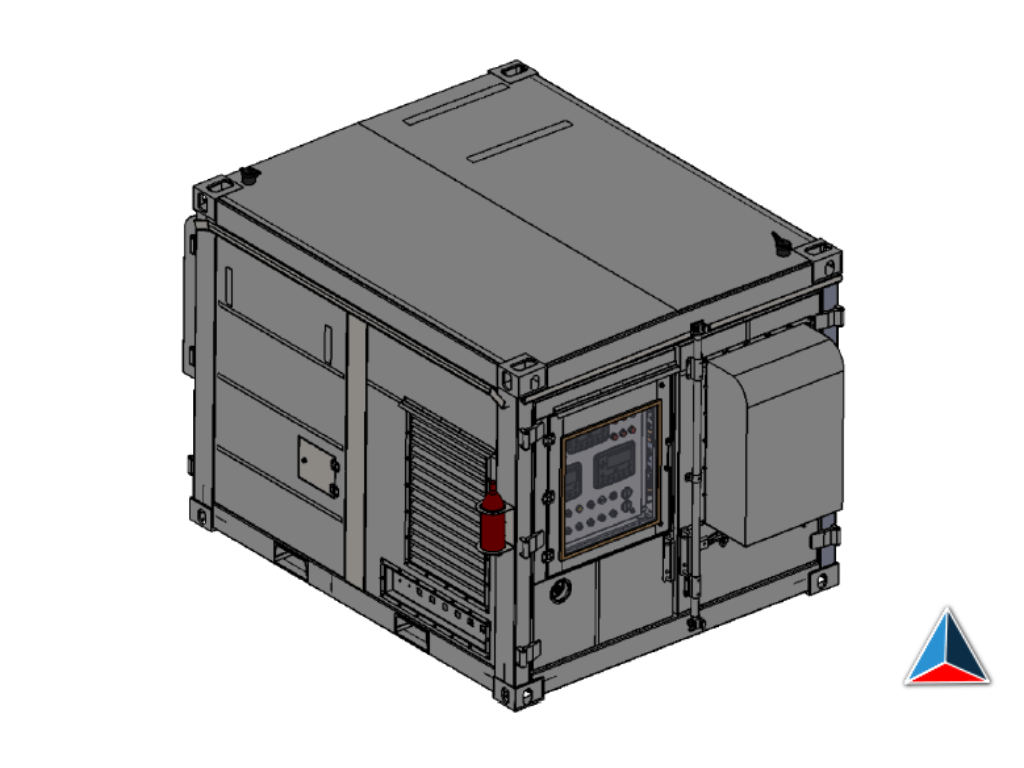
Challenges and Objectives
The client faced significant challenges related to the thermal management of their diesel generator systems. Excessive heat dissipation from components led to temperature hotspots, which could potentially compromise the efficiency and reliability of the system. The primary objectives were:
- To accurately model the 3D geometry of the DG system.
- To define precise boundary conditions, including heat loads in various equipment and ambient air temperature.
- To incorporate material properties and radiator fan details into the analysis.
- To perform steady-state CFD analysis to evaluate temperature, pressure, and velocity distributions.
- To identify temperature hotspots and areas with suboptimal airflow.
- To provide recommendations for improving thermal management and ensuring even temperature distribution.
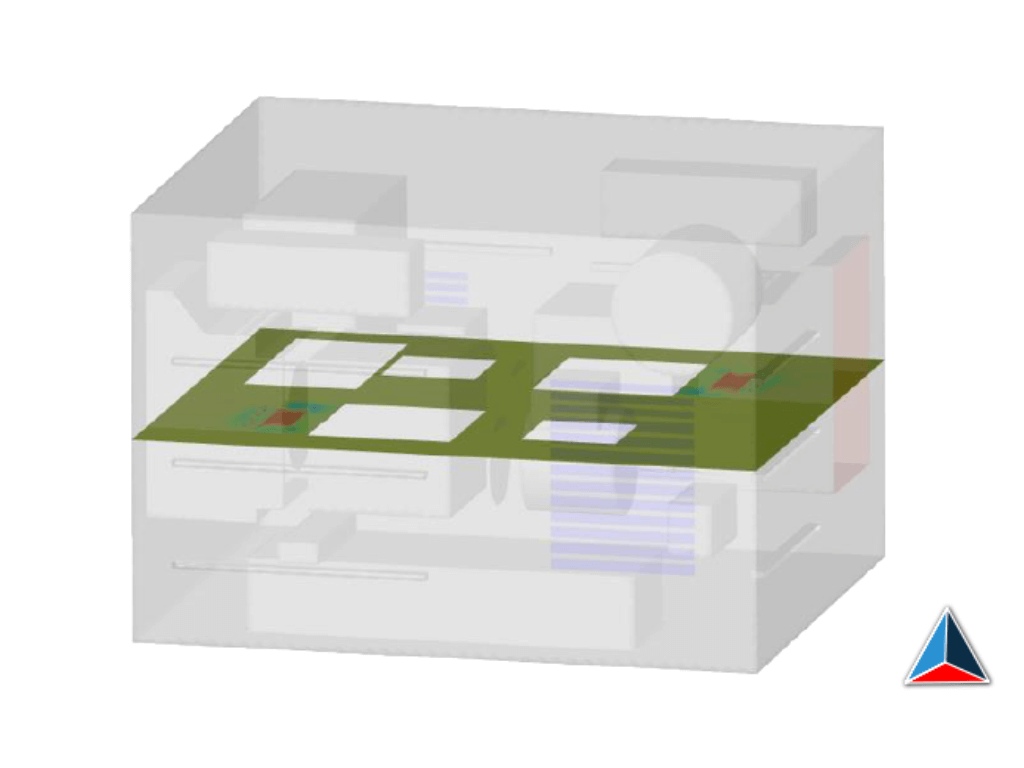
Methodology (Solutions Implemented)
To address the client’s challenges and meet the project objectives, the following methodology was implemented:
- Modeling and Pre-processing:
- The 3D model of the DG system, ensuring accurate representation of all components.
- Boundary conditions were meticulously defined, including heat loads for each piece of equipment, ambient air temperature, and material properties.
- Details of the radiator fan, such as the fan curve, were incorporated to simulate realistic cooling effects.
- CFD Analysis:
- Using advanced CFD tools, a steady-state analysis was performed on the DG system.
- The analysis considered all defined boundary conditions to simulate the thermal behavior of the system.
- Detailed simulations were conducted to evaluate temperature distribution, pressure levels, and airflow velocity within the domain.
- Post-processing:
- Results from the CFD analysis were analyzed to understand the temperature distribution across the system.
- Specific attention was given to identifying temperature hotspots that could lead to potential issues.
- Ambient air velocity distribution around the equipment and within the domain was studied to assess cooling efficiency.
- Pressure distribution within the domain was evaluated to understand the impact on system performance.
BENEFITS (RESULTS ACHIEVED)
The CFD analysis provided the client with critical insights into the thermal management of their diesel generator systems. The key results achieved were:
- Temperature Distribution:
- The analysis revealed the temperature distribution within the system, highlighting areas with excessive heat accumulation.
- Temperature hotspots were successfully identified, enabling targeted improvements to enhance thermal management.
- Airflow Characteristics:
- The study provided a detailed understanding of ambient air velocity distribution across the domain and around the equipment.
- Optimized airflow patterns were identified, suggesting modifications to improve cooling efficiency.
- Pressure Distribution:
- Pressure levels within the domain were evaluated, ensuring they were within acceptable limits to maintain system integrity.
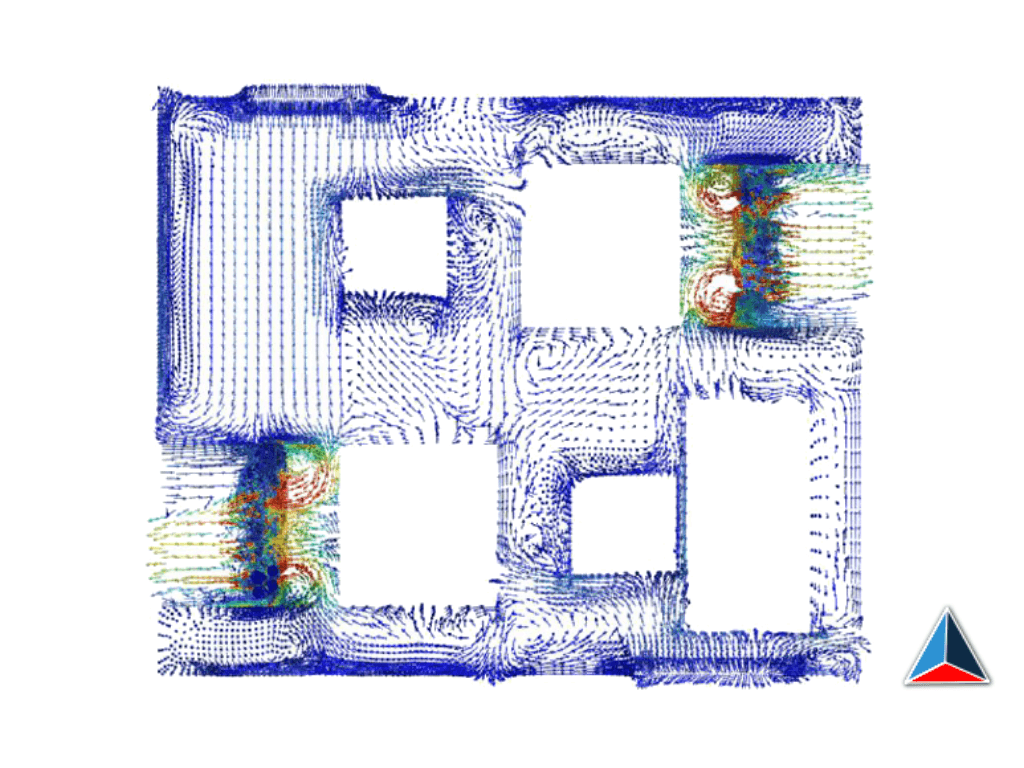
Summary of Project
In conclusion, the CFD analysis of the diesel generator system successfully addressed the client’s thermal management challenges. By accurately modeling the system, defining precise boundary conditions, and performing detailed simulations, the study provided valuable insights into temperature, pressure, and airflow characteristics. The identification of temperature hotspots and the optimization of airflow patterns resulted in enhanced thermal management and improved system performance. The quantifiable improvements achieved through this analysis underscored the importance of CFD in ensuring the reliability and efficiency of diesel generator systems. This case study exemplifies the effective application of CFD techniques to solve complex thermal management issues, providing the client with actionable recommendations for long-term success.